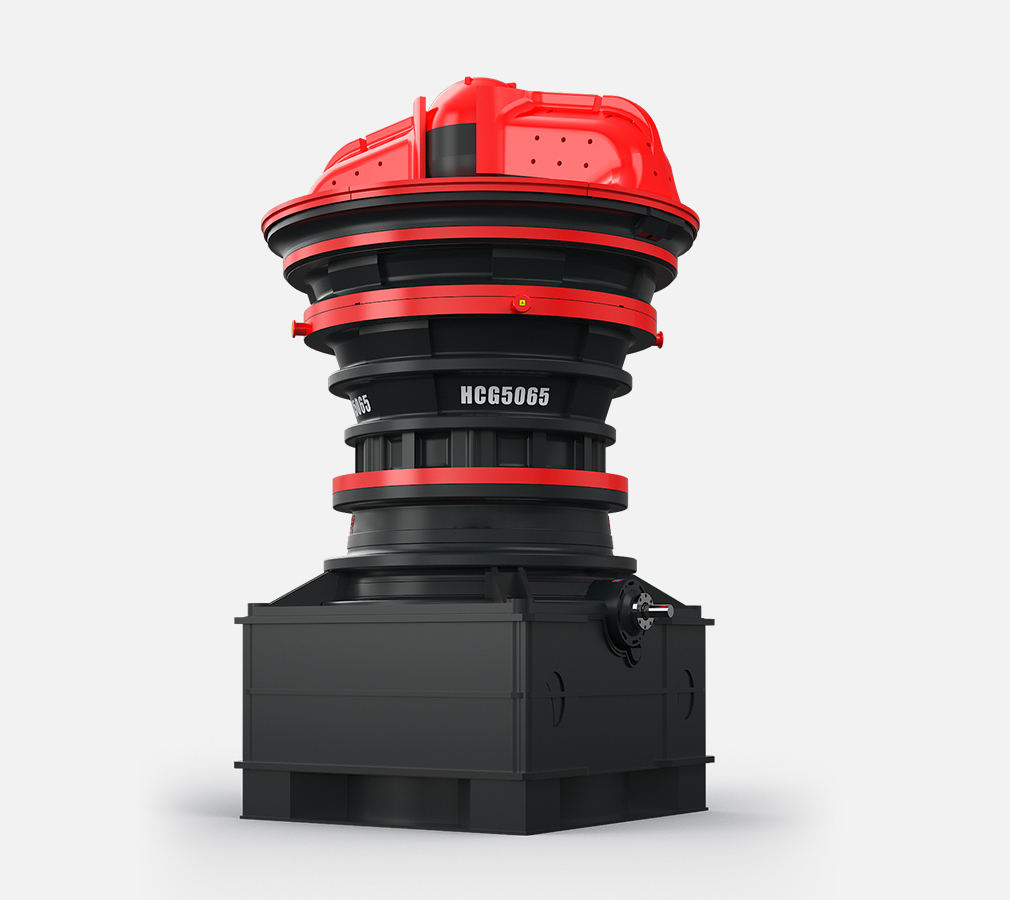
Gyratory crusher is a primary crusher with large capacity and excellent crushing efficiency. It is more suitable for large-scale crushing than a jaw crusher. And its discharging particle size is smaller and the particle shape is better.
Gyratory crushers are often used in the first crushing stage. Together with secondary and tertiary crushers (such as cone crushers, impact crushers, roller crushers, etc.), it can form a complete crushing production line to achieve excellent crushing efficiency.
Get the Latest PriceThe gyratory crusher is suitable for coarse crushing of materials with medium to high hardness and low water content, such as granite, basalt, marble, coal, gold ore, iron ore, gypsum, limestone, etc.
Model | Feeding opening size (mm) |
Max.Feeding size (mm) |
Adjustment range of discharge port (mm) |
Capacity (t/h) |
Power (kw) |
Dimensions L×W×H(mm) |
HCG4265 | 1065 | 900 | 140-175 | 2018-2878 | 400 | 3940×4170×6900 |
HCG5065 | 1270 | 1050 | 150-175 | 2403-2943 | 400 | 4460×4430×7610 |
HCG5475 | 1370 | 1150 | 150-200 | 2893-3493 | 450 | 4930×4925×8410 |
HCG6275 | 1575 | 1350 | 150-200 | 2898-4338 | 450 | 5580×5250×9090 |
HCG6089 | 1525 | 1300 | 165-230 | 4203-5813 | 630 | 5590×5445×10470 |
HCG60110 | 1525 | 1300 | 175-250 | 5543-8898 | 1250 | 6200×5940×11390 |
Note:processing Capacity May Vary With Different Materials And Feeding Sizes.
When the gyratory crusher is working, the eccentric arrangement of the main shaft produces rotational motion, and the materials enter the crushing chamber and are crushed.
Through the adjustment of the hydraulic cylinder, the discharge particle size is changed. Finally, qualified materials are discharged from the bottom opening.
The large-angle crushing cavity, which is 15% larger than similar primary crushers, the long crushing surface and the feed on both sides make the feed particle size unrestricted and have high crushing efficiency and output.
The whole machine adopts durable manganese steel lining plate and crushing head, forged spindle, hydraulic cylinder and lubrication system.
The strength is increased by 70%.
The crushing cavity is evenly worn, which can reduce the number of liner replacements, reduce operating costs, reduce downtime and reduce operating costs.
It is equipped with a standard displacement sensor for the operator to observe the spindle position and machine operating conditions in real time.
It also adopts over-iron protection and fully enclosed structure to ensure the safe and environmentally friendly production.
We collaborate with clients globally to deliver top-notch mineral processing equipment and tailored solutions, aiming to optimize plant efficiency and reduce operating costs. Additionally, we prioritize ESG (Environmental, Social, and Governance) initiatives, actively advocating for the sustainable advancement of eco-friendly mining and recycling sectors.
Based on high quality and perfect after-sales service, our products have been exported to more than 120 countries and regions. FTM Machinery has become the first choice of more than 2,000,000 customers.